Comienza la producción del componente central del eActros 600 en la planta de Mannheim: la caja frontal


Mercedes-Benz Trucks celebrará el inicio de la producción en serie del eActros 600 a finales de noviembre de este año en la planta de Mercedes-Benz en Wörth. El eActros 600 fue elegido recientemente como “Camión Internacional del Año 2025” en la IAA-Transportation en Hannover.
Recibí las noticias en tu celular: Canal de WhatsApp Motorpy
Los primeros vehículos para clientes del eActros 600 se fabricarán y matricularán antes de finales de 2024. En cada vehículo se instalará un componente central de la planta de Mercedes-Benz en Mannheim: la denominada caja frontal.
ACERCA DE LA CAJA FRONTAL


La caja frontal es un complejo módulo tecnológico con varias unidades de control, componentes de alto voltaje y un compresor de aire eléctrico, y se encuentra en el espacio que antes ocupaba el motor de combustión. A diferencia del motor diésel, la caja frontal no tiene una función de accionamiento específica, sino que contiene una gran cantidad de componentes que son esenciales para el funcionamiento del camión. En total, hay más de 1.000 piezas individuales. Acomodar esta gran cantidad de componentes en un espacio muy reducido fue un desafío especial durante el proceso de desarrollo. Al final, esto se logró mediante una denominada “estructura en capas”, en la que los componentes individuales se construyen de abajo a arriba.
Andreas Moch, director de la planta de Mercedes-Benz en Mannheim: «La caja frontal es una unidad de montaje intensivo para vehículos propulsados por batería. Tras una exitosa fase de prototipos, ahora estamos encantados de poder pasar a la producción en serie. Tanto la preparación del chasis como el montaje de todos los componentes individuales y las pruebas de estas unidades se llevan a cabo en la planta de Mercedes-Benz en Mannheim».
Moch continúa: “Nuestra planta de Mercedes-Benz Mannheim es el centro de competencia en tecnología de baterías y sistemas de alto voltaje de Daimler Truck. Con el inicio de la producción de la caja frontal, alcanzamos ya el segundo hito de este año, después de que abrimos nuestro Centro de Tecnología de Baterías en verano. Esto demuestra que estamos bien posicionados en la planta en términos de transformación y estamos haciendo una importante contribución a la configuración de la movilidad sin emisiones del futuro”.
Bruno Buschbacher, presidente del comité de empresa de la planta de Mercedes-Benz en Mannheim: «Estoy muy contento de que hayamos lanzado con éxito el primer producto, la caja frontal, en virtud del acuerdo firmado en 2021, y de que una parte del sistema de propulsión para los motores alternativos se encuentre ahora en Mannheim. Se trata de un paso importante en la transformación de nuestra antigua planta de motores. La gama vertical de fabricación del futuro debe permitirnos seguir produciendo nosotros mismos los componentes esenciales. De cara al futuro, es fundamental seguir invirtiendo en el futuro de la producción de motores y también en nuevos productos y en la formación de los empleados para superar con éxito esta transformación y, de este modo, disponer de puestos de trabajo seguros y atractivos en Mannheim a largo plazo».
ESTRUCTURA DE LA LÍNEA DE MONTAJE


En un edificio de más de 100 años se realizaron importantes reformas durante un año para crear la línea de producción de cajas frontales. Entre otras cosas, se renovaron el revestimiento del suelo de 5.500 m², la ventilación y la iluminación de la nave y se reconstruyó la estructura portante. A continuación se instaló la moderna línea de producción con zona logística, que ofrece un alto grado de flexibilidad para diferentes cantidades, variantes de productos y generaciones posteriores.
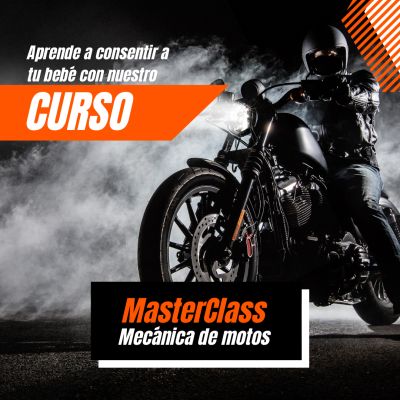
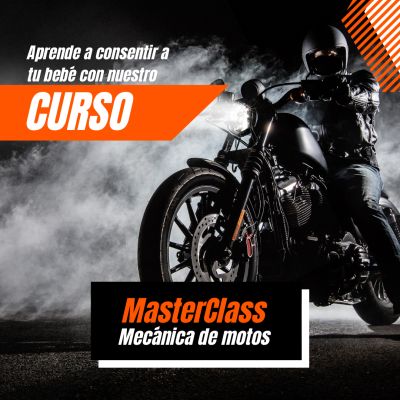
La línea de montaje de la caja frontal consta de cuatro secciones de producción consecutivas. Cada una de estas secciones contiene varias estaciones de montaje, con las zonas de material y estaciones de premontaje correspondientes ubicadas a un lado. Aquí, los niveles individuales de la caja frontal se completan uno tras otro. Después de completar cada nivel, la caja frontal pasa por una llamada puerta de calidad, donde se verifica la ejecución correcta del proceso de montaje antes de construir el siguiente nivel. Una vez que se han superado con éxito todas las puertas de calidad y se ha confirmado la calidad del montaje en la llamada “inspección de final de línea” (inspección EOL), la caja frontal se prepara para su envío a la planta de Mercedes-Benz en Wörth.
FORMACIÓN EN EL NUEVO CENTRO DE FORMACIÓN DE ALTA TENSIÓN DE MANNHEIM


El lema de los mecánicos que fabrican la caja frontal es “el montaje sigue siendo el montaje”, aunque de forma algo diferente a la de los sistemas de propulsión diésel convencionales. El equipo de producción está formado actualmente por 25 empleados, pero esta cifra podría aumentar a 170 en el futuro. Para preparar de forma óptima a los empleados de la planta de Mannheim para los retos de la transformación, desde octubre de este año reciben formación en un nuevo centro de formación de alto voltaje. Este ofrece un entorno de aprendizaje práctico en el que los participantes pueden adquirir conocimientos completos sobre las últimas tecnologías de alto voltaje y baterías. Para ello se utilizan métodos de enseñanza innovadores, como gafas de realidad virtual y tecnología de realidad aumentada.
OTROS COMPONENTES CLAVE DE GAGGENAU Y KASSEL
Las plantas de Gaggenau y Kassel, que forman parte de la red de producción y tecnología de componentes de propulsión eléctrica y sistemas de baterías de Daimler Truck, también suministrarán componentes clave para el eActros 600. La planta de Mercedes-Benz en Gaggenau, el centro de competencia para componentes de propulsión eléctrica, fabricará componentes de transmisión como ejes y engranajes, así como piezas de carcasa. Estos se entregarán a la planta de Mercedes-Benz en Kassel, el centro de competencia para ejes convencionales y sistemas de propulsión eléctrica. Los componentes de ejes y transmisión se ensamblarán íntegramente aquí.
ACERCA DEL EACTROS 600
El eActros 600 para el transporte de larga distancia se estrenó mundialmente a finales de 2023. La elevada capacidad de la batería de más de 600 kilovatios hora [1] (de ahí la denominación del modelo 600) y un nuevo eje de propulsión eléctrica especialmente eficiente desarrollado internamente permiten que el camión eléctrico alcance una autonomía de 500 kilómetros [2] sin carga intermedia. Esta autonomía se consigue en condiciones muy realistas y prácticas con una masa bruta combinada de 40 toneladas, y también se puede superar considerablemente en función del estilo de conducción y la ruta. El eActros 600 podrá incluso recorrer más de 1.000 kilómetros al día. La carga intermedia durante las pausas legales del conductor, incluso sin carga de megavatios, lo hace posible, siempre que haya opciones de carga disponibles. Además de la carga CCS con hasta 400 kW, el eActros 600 también permitirá más adelante la carga de megavatios (MCS).
ACERCA DE LA PLANTA DE MERCEDES-BENZ EN MANNHEIM
En 1908 se fundó en Mannheim-Waldhof, junto al río Luzenberg, la actual planta de Mercedes-Benz en Mannheim. En esta planta trabajan más de 4.600 personas que producen motores y componentes relacionados para vehículos industriales. Además, es el centro de competencia de Daimler Truck para tecnologías de baterías y sistemas de alto voltaje, que contribuye de forma significativa a la producción en serie de la gama de productos electrificados. En el centro de tecnología de baterías se encuentra una línea piloto propia para la producción de prototipos de celdas de batería. Aquí, el equipo de desarrollo trabaja en el desarrollo de conceptos y sistemas de montaje para paquetes de baterías. La fundición de la planta es uno de los principales fabricantes mundiales de piezas de fundición de hierro para vehículos. Además, en el llamado centro europeo de producción de motores de intercambio se remanufacturan motores para vehículos industriales y turismos.
En Mannheim también se encuentra la planta de Daimler Buses, que es el centro de competencia para autobuses urbanos de todos los tipos de propulsión y forma parte de la red de producción de Daimler Buses. Entre otros vehículos, de la línea de producción de esta planta salen el autobús urbano totalmente eléctrico eCitaro y el eCitaro Fuel Cell con pila de combustible a base de hidrógeno para ampliar la autonomía. Desde 2024, la planta está preparada para producir autobuses urbanos 100 % eléctricos.
La formación y la retención de jóvenes talentos también son igualmente importantes para la sede de Mannheim: con más de 100 años de experiencia, los jóvenes se forman aquí: un total de más de 11.000 jóvenes han completado su formación aquí.
[1] El eActros 600 tiene tres paquetes de baterías, cada uno con 207 kWh. Estos ofrecen una capacidad instalada total de 621 kWh. Capacidad nominal de una batería nueva, basada en condiciones marco definidas internamente. La autonomía puede variar según la aplicación específica y las condiciones ambientales.
[2] El rango se determinó internamente bajo condiciones de prueba específicas, después del preacondicionamiento con un tractor semirremolque 4×2 con una masa bruta combinada de 40 t a una temperatura exterior de 20 °C en una operación de transporte de larga distancia, y puede desviarse de los valores determinados de acuerdo con el Reglamento (UE) 2017/2400.