Industrial Metaverse de Renault do Brasil aplica tecnologías avanzadas en el proceso de producción
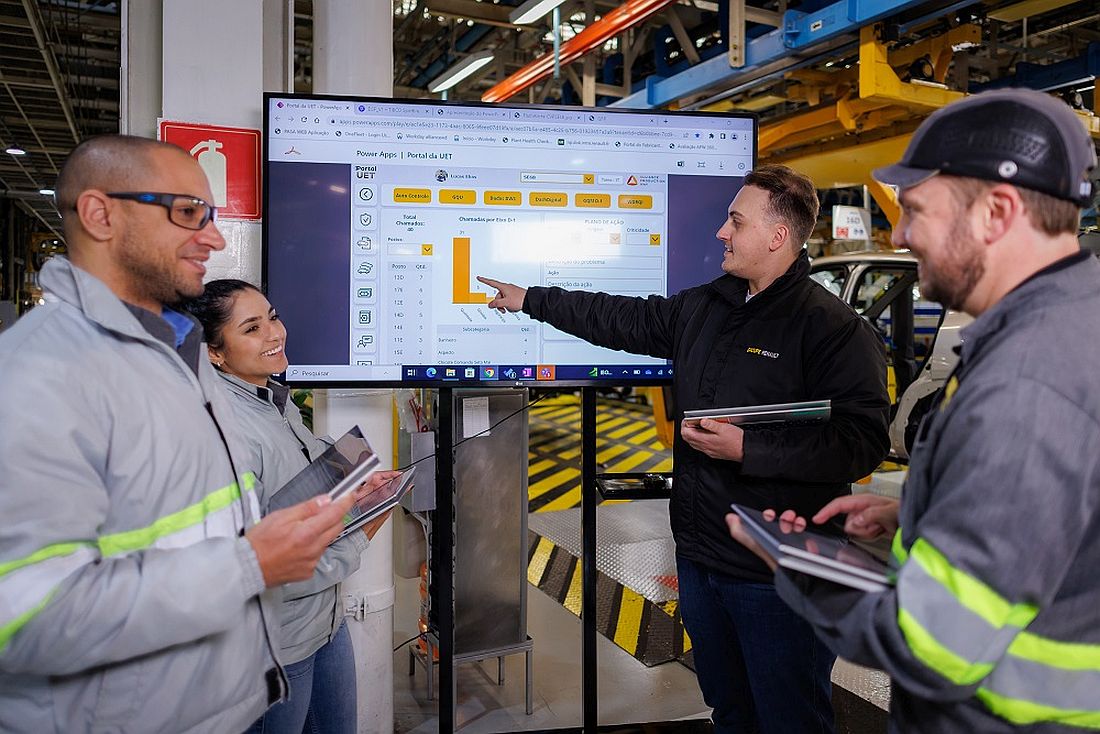
La inteligencia artificial, el gemelo digital, las máquinas y estaciones de trabajo conectadas, la recopilación masiva de datos con foco en el rendimiento y la impresión 3D son algunas de las soluciones ya implementadas en el Metaverso Industrial de Renault.
Recibí las noticias en tu celular: Canal de WhatsApp Motorpy
El Complejo Ayrton Senna, que alberga las fábricas de Renault do Brasil, fue reconocido por el Foro Económico Mundial (WEF) como “Faro de la 4ª Revolución Industrial Avanzada (4IR)” – “Faro de la 4ª Revolución Industrial Avanzada”, por ser un planta de referencia en actuaciones de industria 4.0.
Renault do Brasil aplica tecnologías avanzadas en el proceso de producción desde el inicio de la producción en Brasil, en 1998, hace 25 años. Fue el primer fabricante de automóviles en Brasil, y la primera unidad de Renault en el mundo, en adoptar pintura a base de agua y diseñó todo el Complejo Ayrton Senna, un área de 2,5 millones de metros cuadrados, el 40% de los cuales está cubierto de bosque. conservados, con las más avanzadas tecnologías de producción.
El Grupo Renault, por su parte, tiene el 100% de sus líneas de producción conectadas (8.500 equipos), el 90% de sus flujos de suministro están permanentemente monitorizados y el 100% de sus datos clave de la Cadena de Suministro están alojados en el Metaverso del Grupo Renault, con una verdadera réplica del mundo físico monitoreado en tiempo real.
Y Renault do Brasil sigue este camino de innovación constante, con su Metaverso Industrial, donde aplica las tecnologías más avanzadas en el proceso industrial, como inteligencia artificial, máquinas y estaciones de trabajo conectadas, gemelos digitales, minería de datos, impresión 3D y AGVs, automatizados. vehículos guiados, entre otras soluciones, del mismo modo que el Grupo Renault aplica en otras unidades del mundo.
Este Metaverso ofrece seguimiento a través de una mejor visibilidad del ambiente de trabajo, permitiendo que los distintos actores ganen agilidad y autonomía en la toma de decisiones. Esto hace que la tecnología sea una parte omnipresente de cada paso del proceso de producción de vehículos y convierte a Renault en el único fabricante de automóviles en América Latina será reconocida por el Foro Económico Mundial (WEF) como “Faro de la 4ª Revolución Industrial Avanzada (4IR)” – “Faro de la 4ª Revolución Industrial Avanzada”, por ser una planta de referencia en acciones de industria 4.0.
“La adopción de las tecnologías avanzadas que componen el Metaverso Industrial de Renault en nuestras fábricas no solo hace más eficiente el proceso de producción, sino que mejora la calidad final de nuestros productos, además de garantizar un control preciso y en tiempo real de todas las etapas de producción. producción de un automóvil”, explica Ricardo Gondo, presidente de Renault do Brasil.

UNA EVOLUCIÓN CONSTANTE

El Metaverso Industrial de Renault do Brasil comenzó en 2016, con la implementación de toda la infraestructura Wi-Fi en las fábricas, en un área de 6.000 metros cuadrados, permitiendo la conectividad en toda la planta.
“Desarrollar la infraestructura adecuada para garantizar que todas las áreas de las fábricas estuvieran conectadas fue el primer paso de Renault do Brasil para sumergirse en el Metaverso Industrial”, explica Caio Nogueira, CIO de Renault Latinoamérica.
Esta estructura fue fundamental para iniciar la digitalización y conectividad de toda la producción en el Complejo Ayrton Senna, donde, actualmente, cuatro mil profesionales trabajan directamente en la fabricación, produciendo 60 vehículos de pasajeros y 15 utilitarios por hora.
Al mismo tiempo, se inició la adopción de aplicaciones digitales y el uso de tabletas para el 100% del equipo de dirección de producción, eliminando el papel como herramienta de control del proceso productivo, lo que representa un ahorro de 2,5 millones de hojas de papel. Entre 2019 y 2021, Renault comenzó a explorar los datos recopilados por el sistema, tanto para el control de la Cadena de Suministro como para el rendimiento energético y las emisiones de carbono, y ya tenía el 80% de los procesos escaneados. Industrial Metaverse de Renault actualmente mueve mil millones de datos al día a través de todos los sistemas conectados en el mundo.
Toda esta infraestructura le permite a Renault una mayor confiabilidad en el proceso, que converge en la calidad, tanto en el proceso de producción para el operador, que tiene acceso a capacitación digital, estaciones de trabajo conectadas, como en el producto entregado a los clientes, que es monitoreado en toda la producción. escenarios, con tecnologías innovadoras. Esto también permite un seguimiento más preciso y digital de cada vehículo.
“El objetivo final de Metaverso Industrial es que los clientes de Renault reciban un producto de alta calidad percibida, monitoreado de manera precisa y eficiente en todas las etapas de producción”, explica Giuliano Eichmann, director de ingeniería de procesos de Renault do Brasil. “Además, con esta digitalización de la industria, invertimos en investigación y desarrollo en Brasil y contribuimos a formar una fuerza de trabajo extremadamente calificada, conectada y preparada para una nueva revolución industrial”, agrega.
HOY, EL METAVERSO INDUSTRIAL DE RENAULT PERMITE:

· Gestión de alrededor de 700 robots, que contribuyen a mejorar el rendimiento y la calidad en todo el complejo industrial;
· Procesando más de 26.000 imágenes cada día utilizando Inteligencia Artificial;
· Impresión de más de 10.000 piezas al año para Renault do Brasil en el Centro de Impresión 3D;
· El control de más de 346 Vehículos Autoguiados, que aumentan la agilidad y el rendimiento en la fabricación;
· La tecnología Digital Twin implementada en la línea de ensamblaje de ruedas, que fue la primera de su tipo desarrollada dentro del Grupo Renault y se ha convertido en un verdadero cambio de juego cuando se trata de análisis de datos en tiempo real.
“Más que tener herramientas y tecnologías disponibles, todo el proceso de innovación que llevamos a cabo en Renault tiene una verdadera implicación de las personas, que son efectivamente parte de este proceso y que dan sentido a esta cultura de innovación implantada”, explica Vagner Mansan, director de las fábricas de vehículos Renault do Brasil.
A continuación, conozca las principales tecnologías adoptadas en el Metaverso Industrial de Renault do Brasil:
DATOS PARA LA EXCELENCIA EN LA FABRICACIÓN

Al integrar y conectar máquinas, Industrial Data Management (IDM4.0) le permite recopilar, almacenar en Google Cloud y organizar datos, lo que hace que las fábricas sean más inteligentes. Todos estos datos almacenados permiten realizar análisis predictivos que mejoran la toma de decisiones en el proceso industrial.
Exploración de datos enfocada en el desempeño de vanguardia en la cadena de suministro.
Actualmente, el 100 % de los datos clave del proceso se transmiten desde los sistemas de cadena de suministro del Grupo Renault y se almacenan en Google Cloud. Esta fuente infinita de información es accesible a todos los usuarios del proceso de la cadena de suministro, tanto para el flujo de piezas donde tenemos la capacidad de controlar en tiempo real la ubicación de los transportes nacionales y la trazabilidad de los contenedores/barcos en los transportes internacionales, como para el flujo de entrega de vehículos a los concesionarios utilizando tecnologías como la geolocalización. Además, se desarrollan algoritmos que aportan rendimiento a los procesos, optimizando la ocupación de cargas, perfeccionando el desplazamiento de los medios utilizados en la cadena de suministro.
La tecnología también se aplica en la ingeniería de embalaje industrial, utilizando herramientas 3D para simular todos los escenarios en un entorno virtual antes de la validación física.
Rendimiento energético y consumo de recursos en tiempo real
Para acelerar el aprendizaje colectivo sobre el rendimiento energético y el consumo de recursos como agua, electricidad y fluidos industriales, los datos están disponibles para los equipos en tiempo real, lo que permite un mayor control del uso de los recursos.
ESTACIÓN DE TRABAJO DIGITAL CONECTADA (DWS)

La estación de trabajo digital (DWS) permite a los operadores garantizar el cumplimiento de la estación de trabajo:
- Los operadores hacen clic en “OK START” cuando inician su estación de trabajo para verificar todos los requisitos previos necesarios.
- Durante la producción, el sistema puede proporcionar toda la información necesaria (vehículo actual, próximo vehículo, diversidades inusuales, etc.)
- Si es necesario, los operadores pueden solicitar ayuda e informar problemas de calidad: todas las solicitudes se transmiten de inmediato a los líderes de producción.
LÍDER DE LA PRODUCCIÓN

· El Líder de Producción visualiza todos los eventos en tiempo real y toma las decisiones adecuadas independientemente de su ubicación, conectado a través de un dispositivo electrónico, eliminando el papel en el proceso de gestión de operaciones;
· El sistema ahorra tiempo y mejora la sincronización con nuestros clientes;
· Es posible utilizar herramientas adicionales del sistema, como solución de problemas, observación de estaciones de trabajo, mejores prácticas, entre otras.
· El sistema ahorra tiempo y mejora la sincronización con nuestros clientes;
· Es posible utilizar herramientas adicionales del sistema, como solución de problemas, observación de estaciones de trabajo, mejores prácticas, entre otras.
ENTRENAMIENTO DE REALIDAD VIRTUAL

Otra solución adoptada en Renault do Brasil es la formación de los empleados en un entorno de realidad virtual. El proceso se adopta en la formación de operadores de líneas de montaje y pintura, utilizando modelos tridimensionales que pueden ser manipulados virtualmente, utilizando gafas de realidad virtual.
La inmersión en realidad virtual que se realiza durante la formación de los empleados hace que el proceso de formación sea 100% seguro, libre de los riesgos potenciales expuestos en una línea de producción.
GEMELO DIGITAL
La tecnología Digital Twin replica, en un entorno digital, el universo real de la línea de producción. De forma remota, el operador puede ver todo el proceso de producción en tiempo real, e incluso puede realizar cambios en el proceso, o incluso solicitar mantenimiento en la línea real. Con el Gemelo Digital también es posible simular futuros procesos productivos, optimizar las etapas y garantizar una mayor agilidad en la línea de producción.
El proceso Gemelo Digital fue creado en sociedad con investigadores de universidades de Paraná, FIEP y Fundação Araucária y fue inicialmente aplicado en la línea de montaje de ruedas de Renault do Brasil. La tecnología sigue evolucionando y se ha incorporado al Metaverso Industrial de Renault, siendo exportada a otras unidades de la marca en todo el mundo.
INTELIGENCIA ARTIFICIAL
La inteligencia artificial (IA) también se incorporó al proceso de producción de Renault do Brasil. Después de ensamblar el tren motriz, los robots realizan una verificación automática de la estructura para verificar que el proceso se haya desarrollado según lo prescrito. La verificación utiliza IA, que procesa imágenes de referencia para realizar la verificación del ensamblaje real. Cada día se procesan 26.000 imágenes mediante Inteligencia Artificial.
VEHÍCULOS DE GUIADO AUTOMÁTICO (AGV)
Para facilitar y agilizar el proceso productivo, la sustitución de piezas y el transporte de herramientas entre unidades se realizan, en su mayor parte, mediante AGV (Vehículos de Guiado Automático). Disponen de rutas programadas y controladas que garantizan la llegada de los componentes a los destinos correctos, garantizando la programación de las plantas de producción. Actualmente, hay más de 346 AGV circulando por las cuatro fábricas del Complejo.